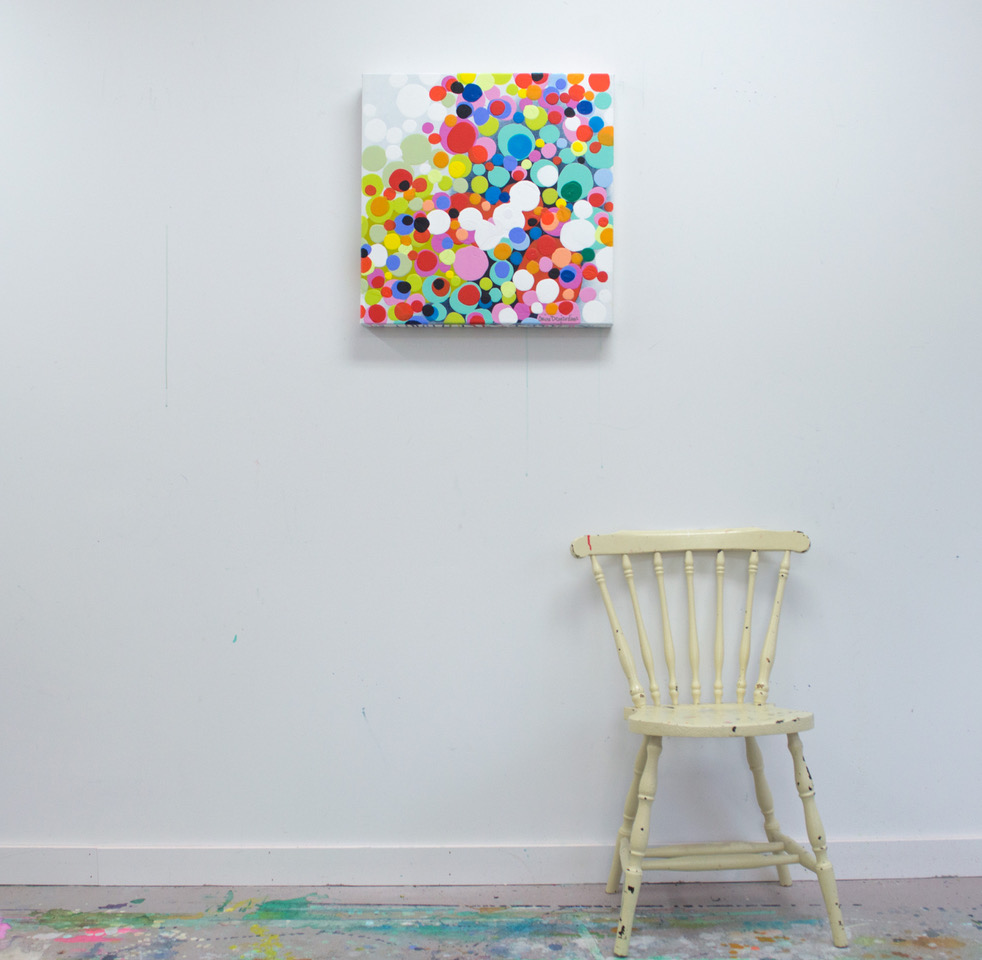
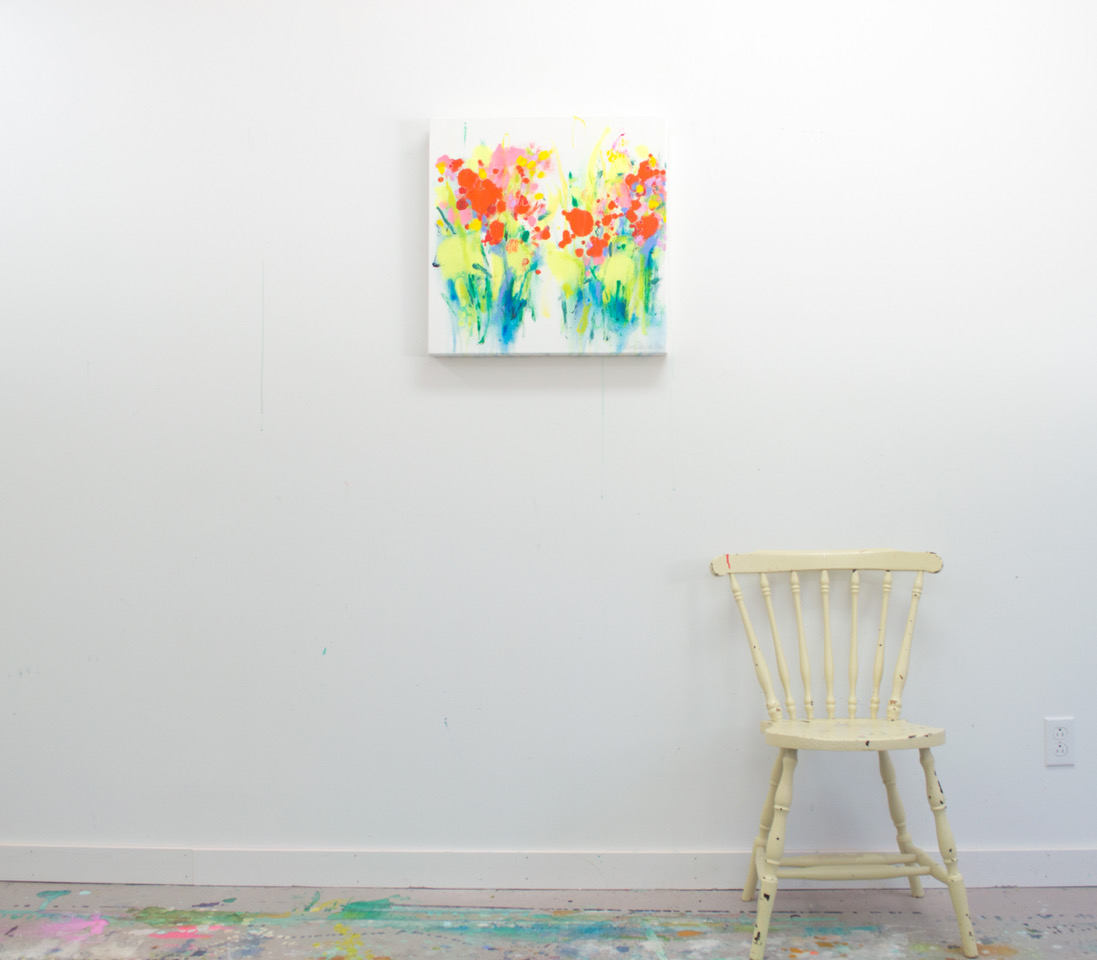
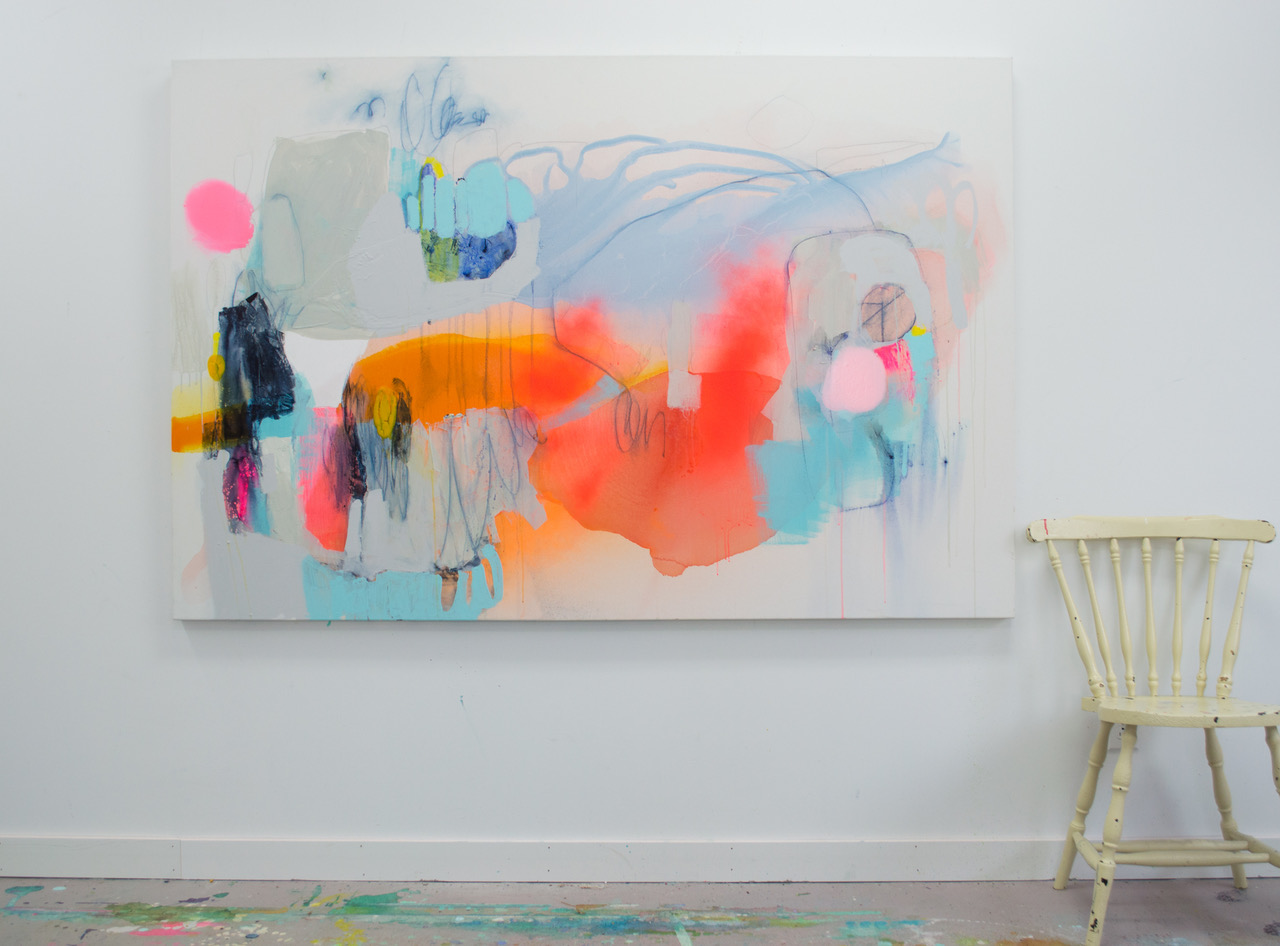
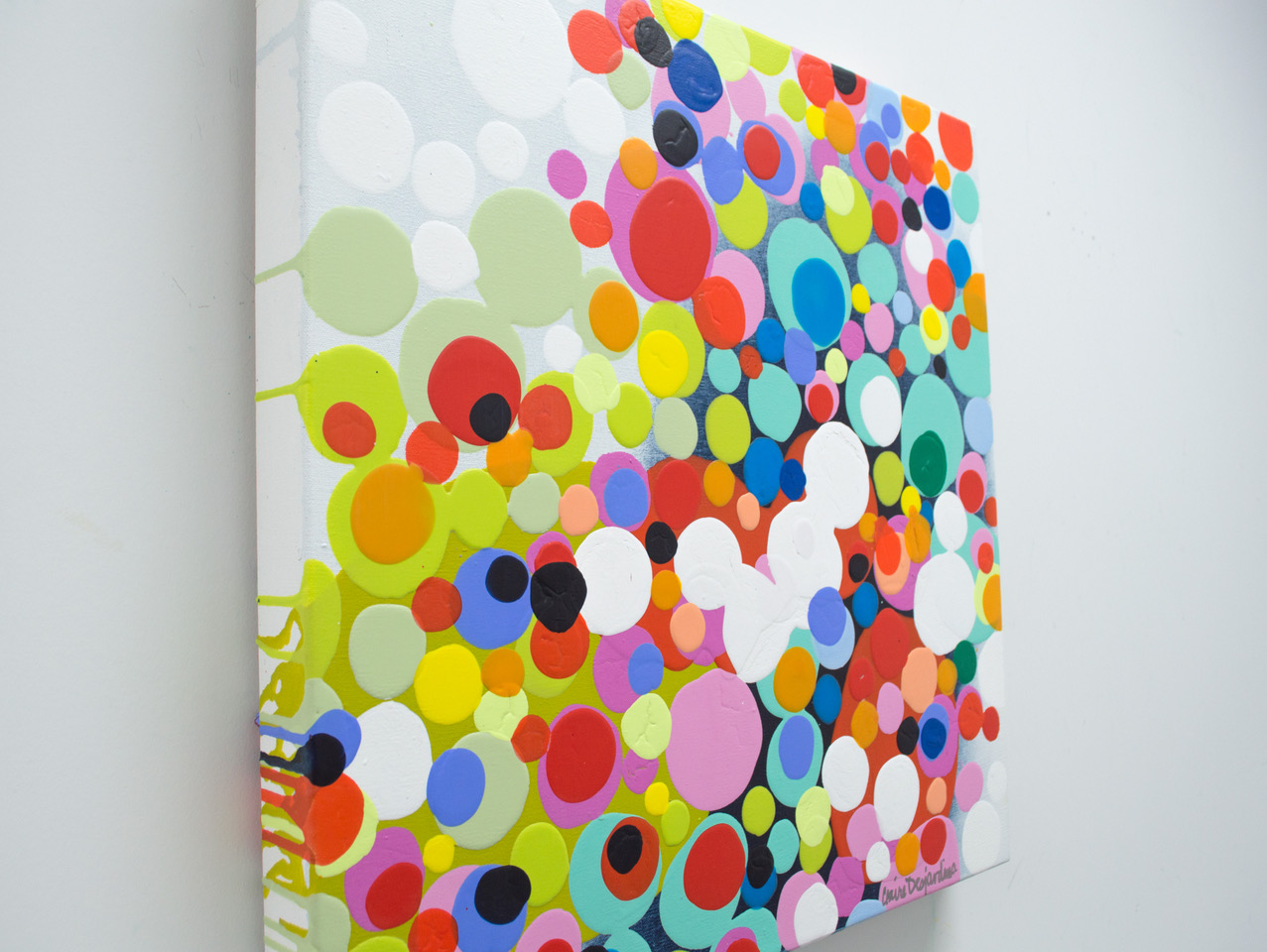
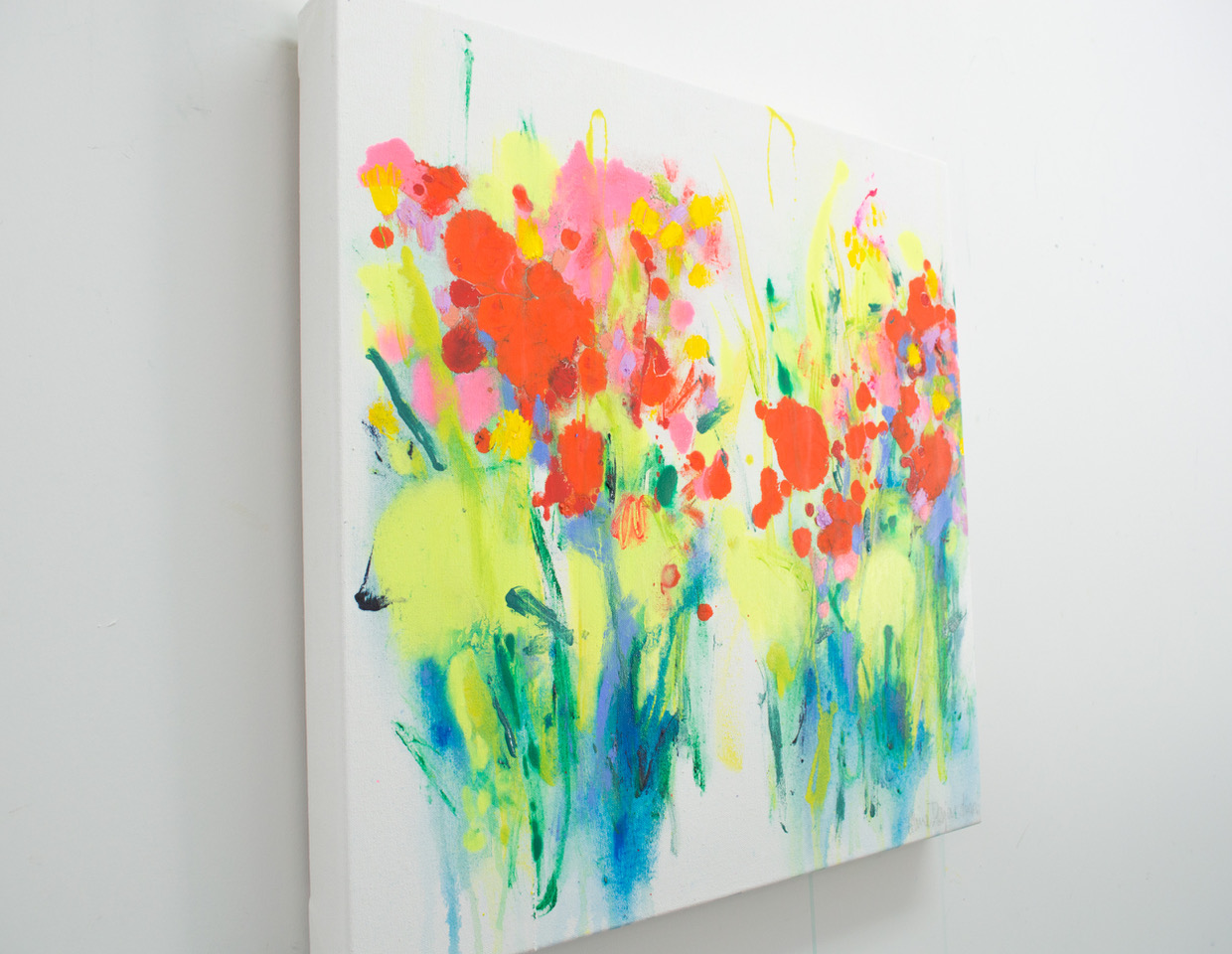
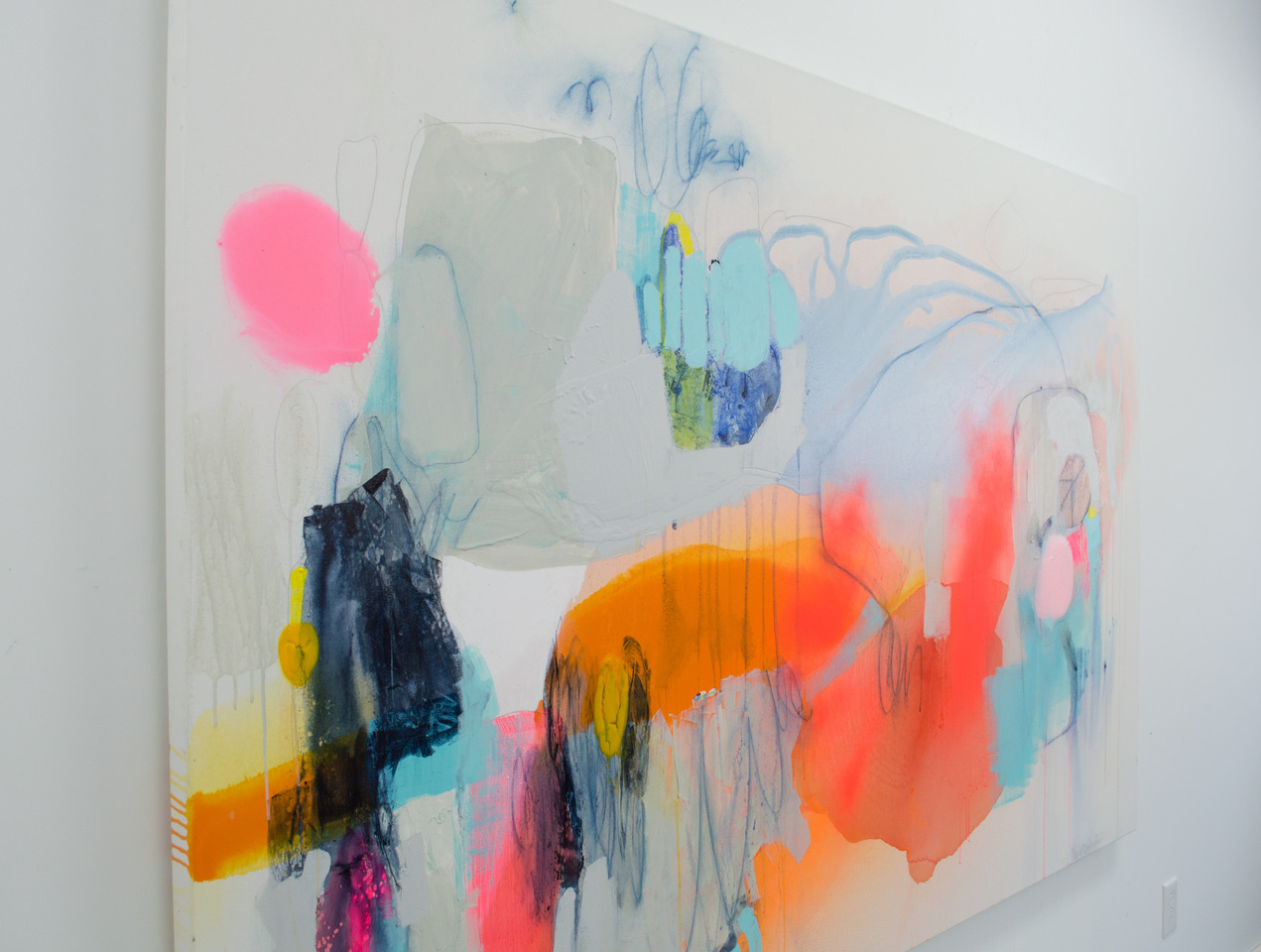
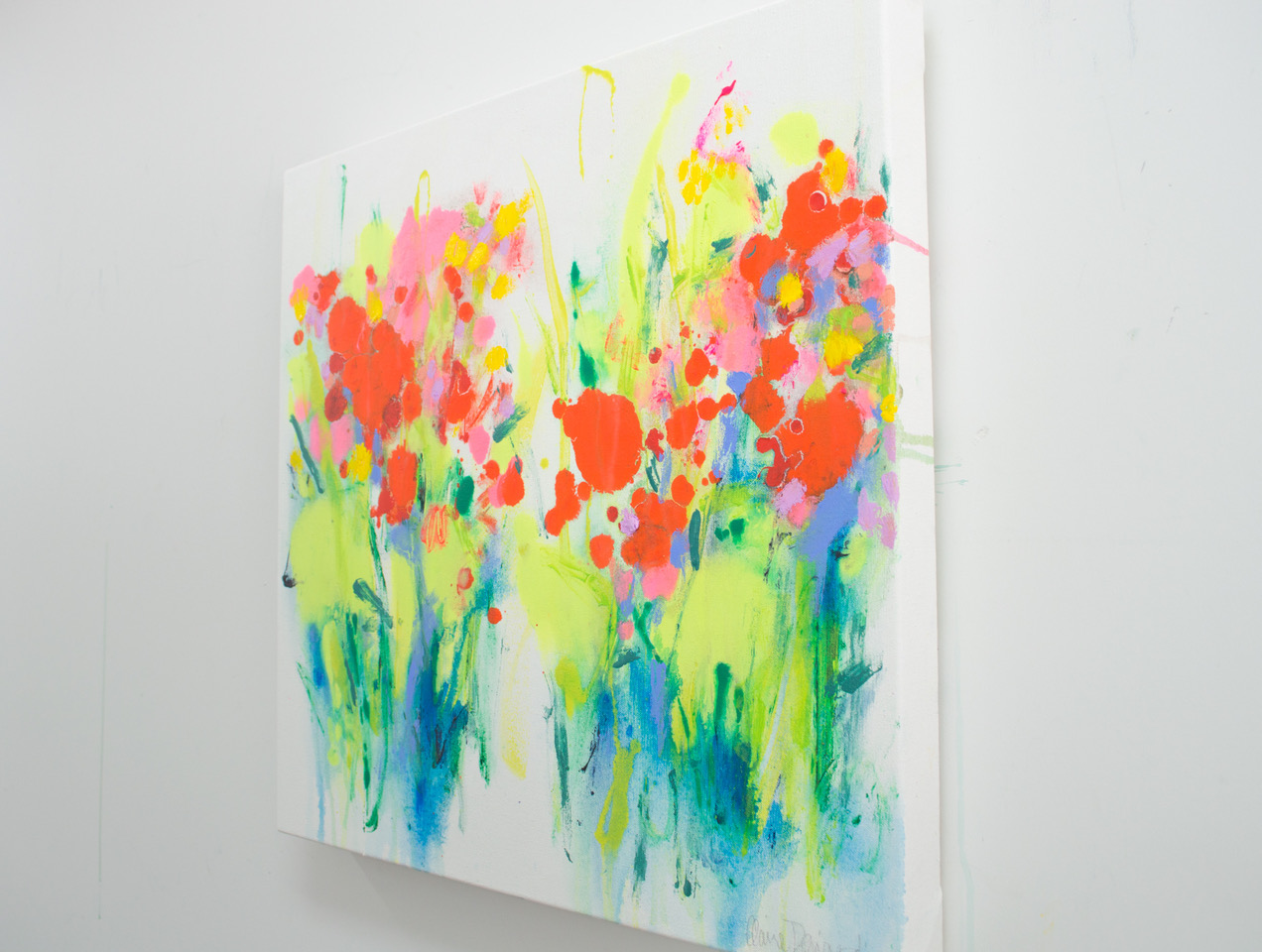
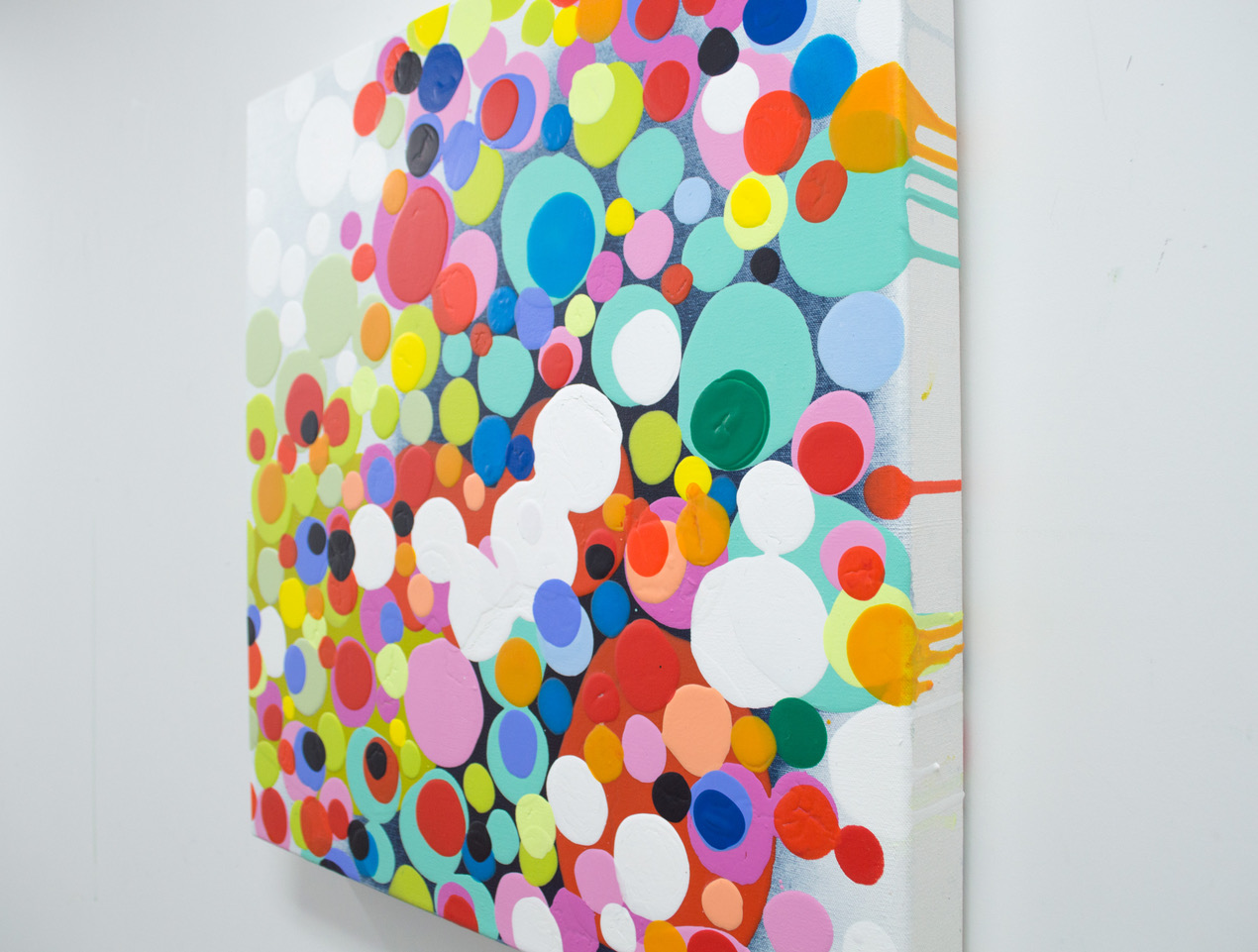
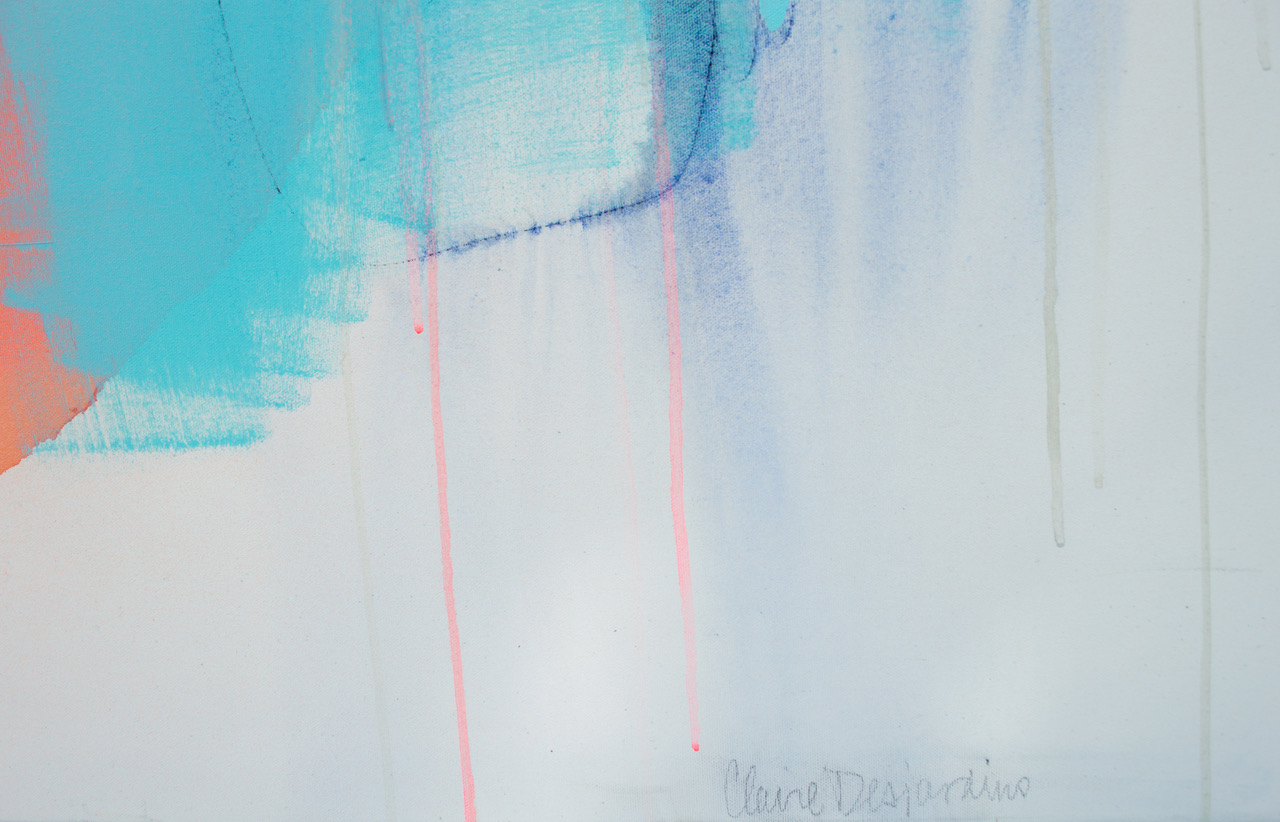
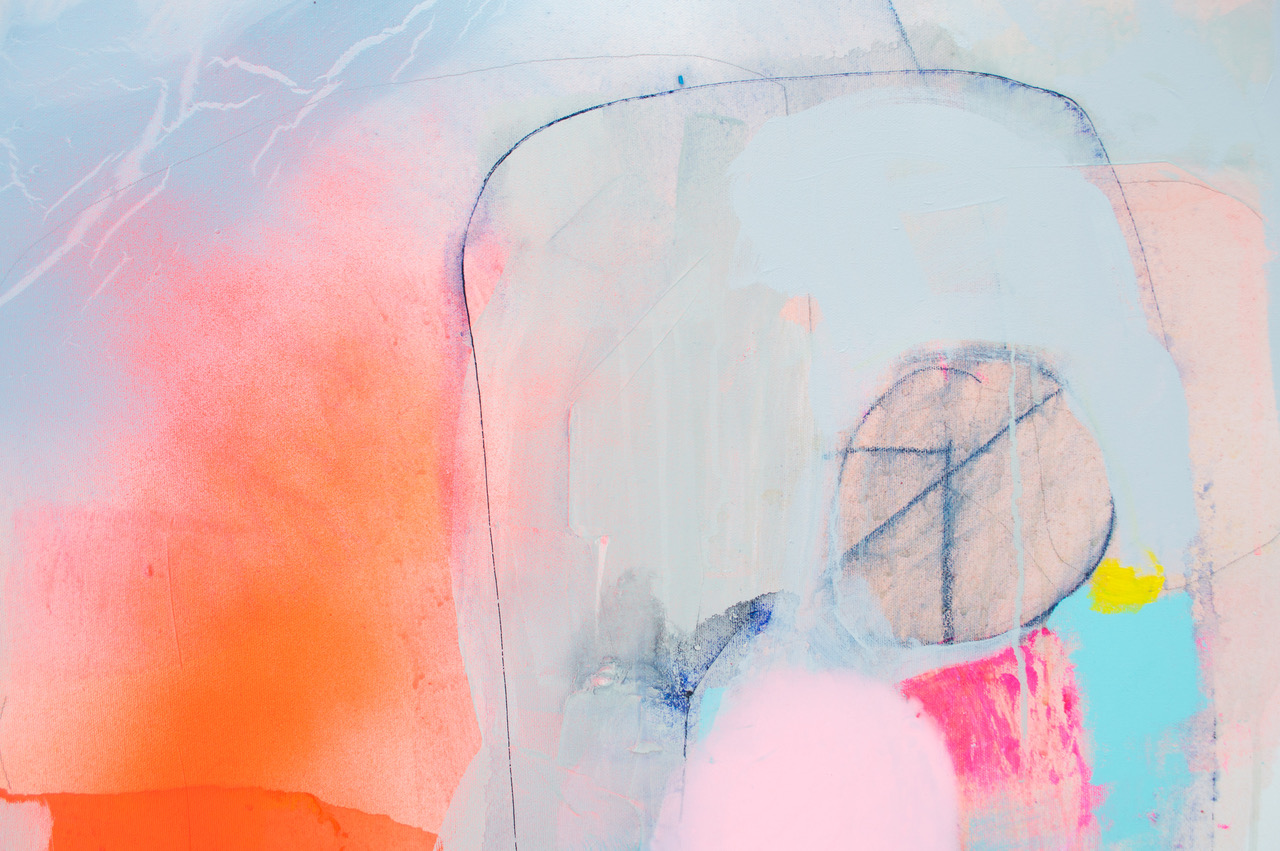
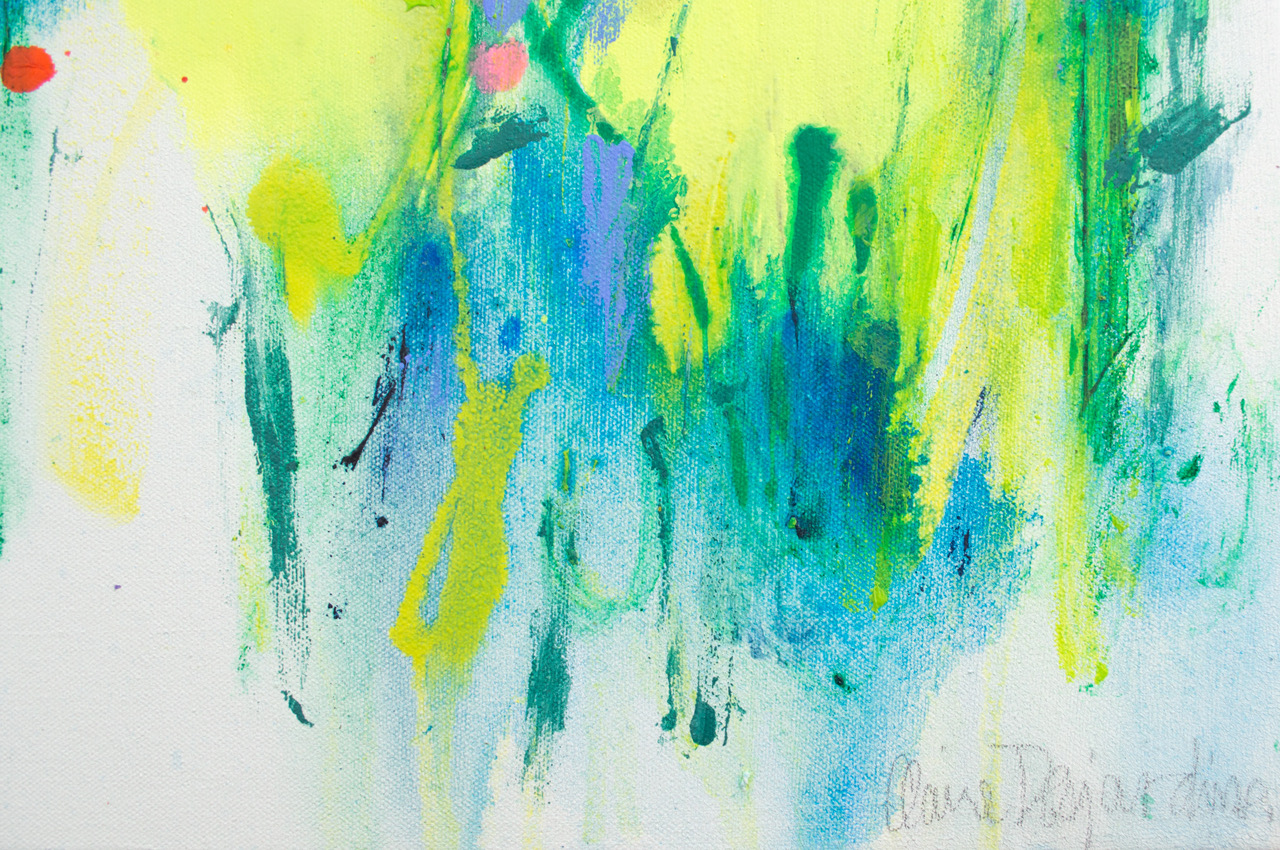
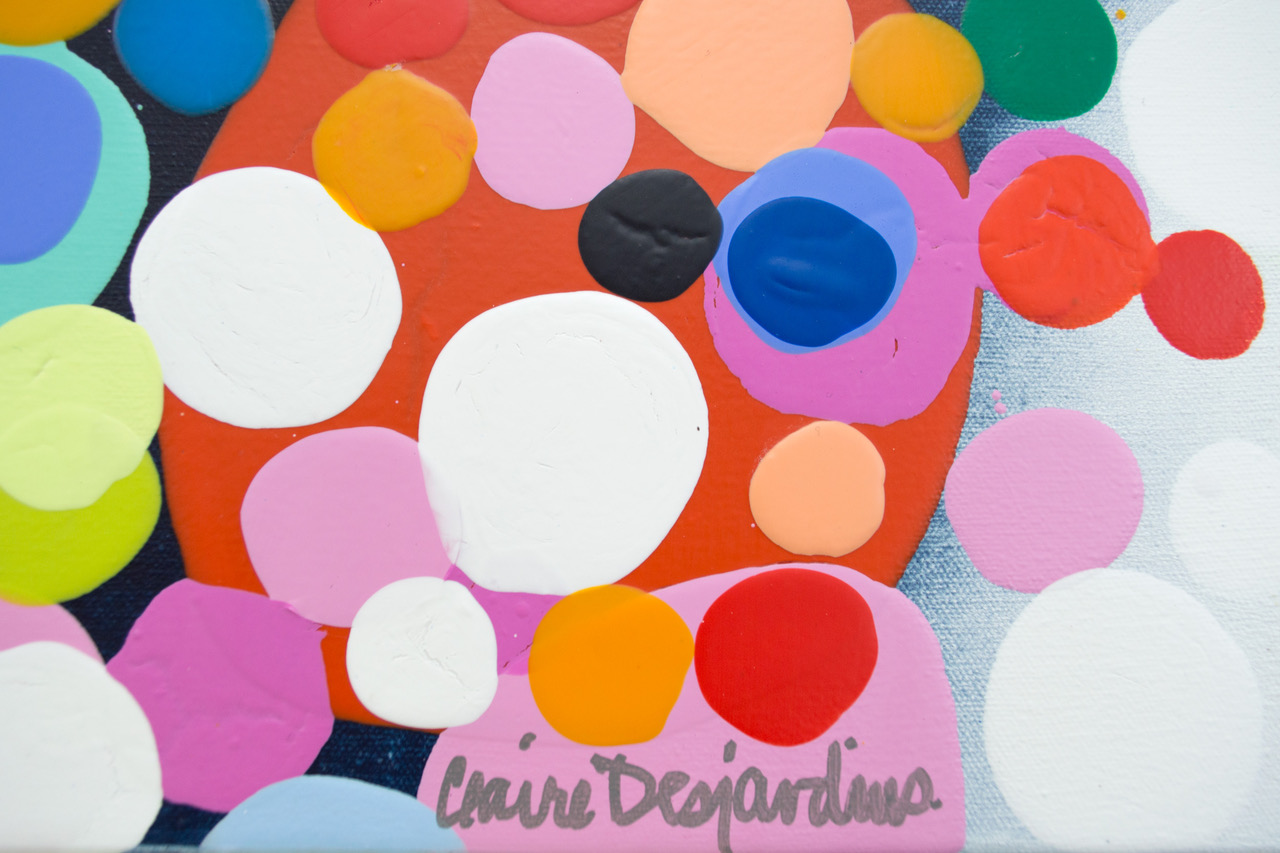
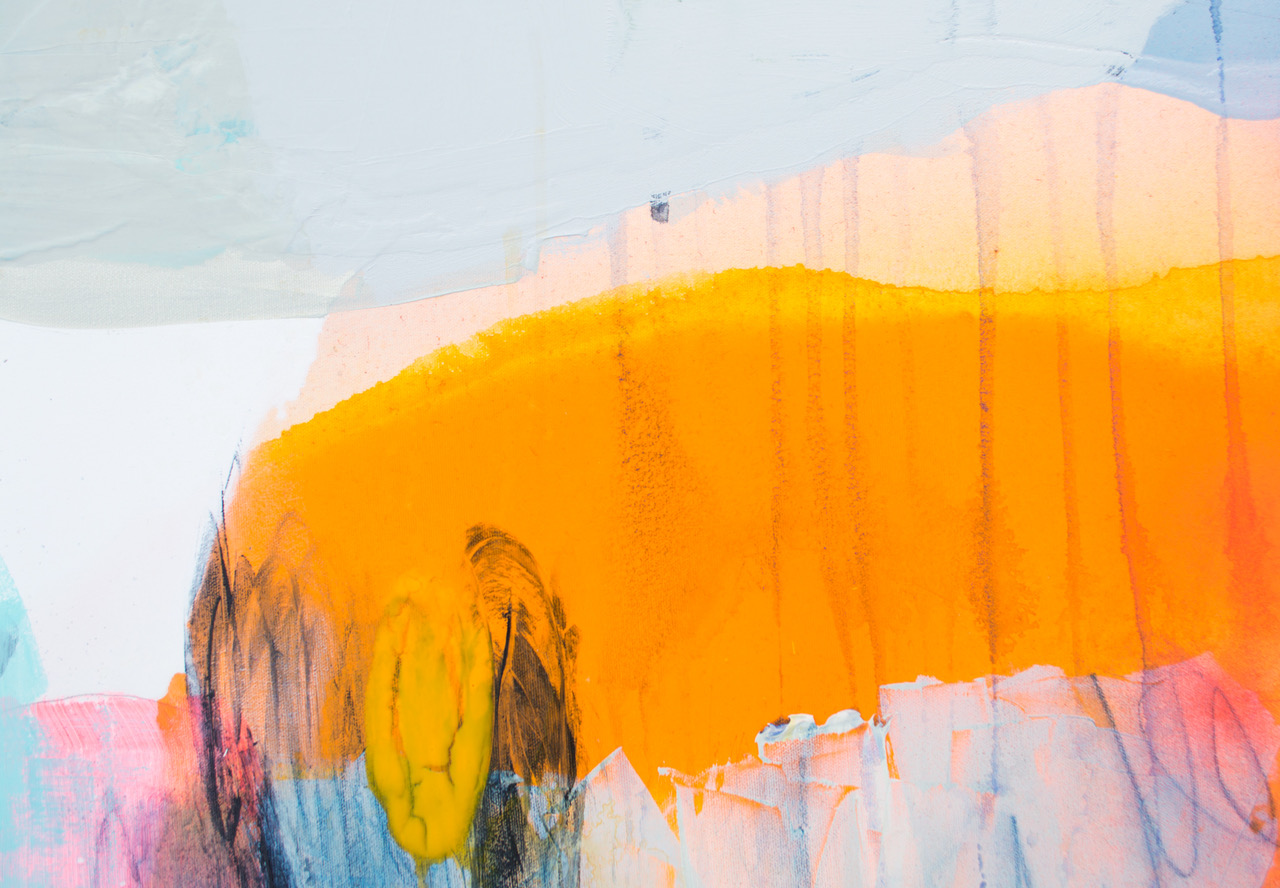
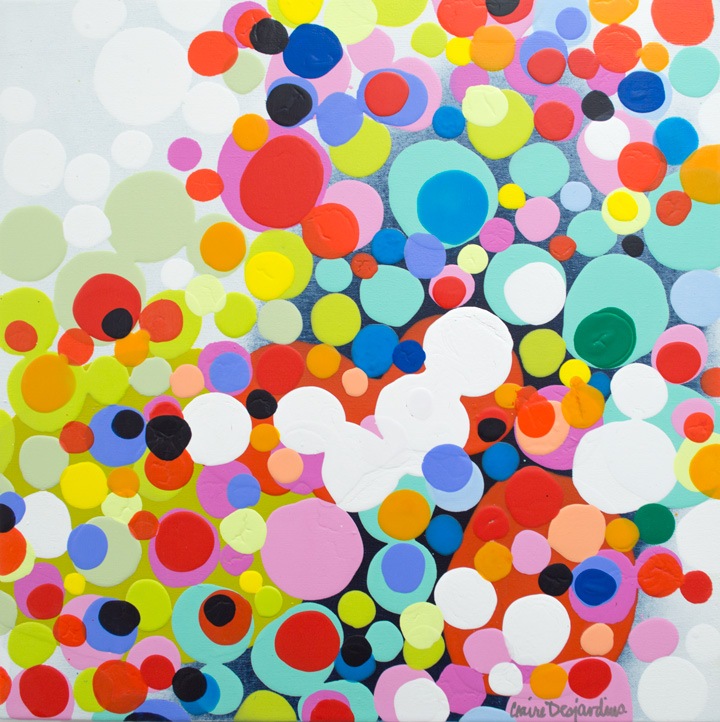
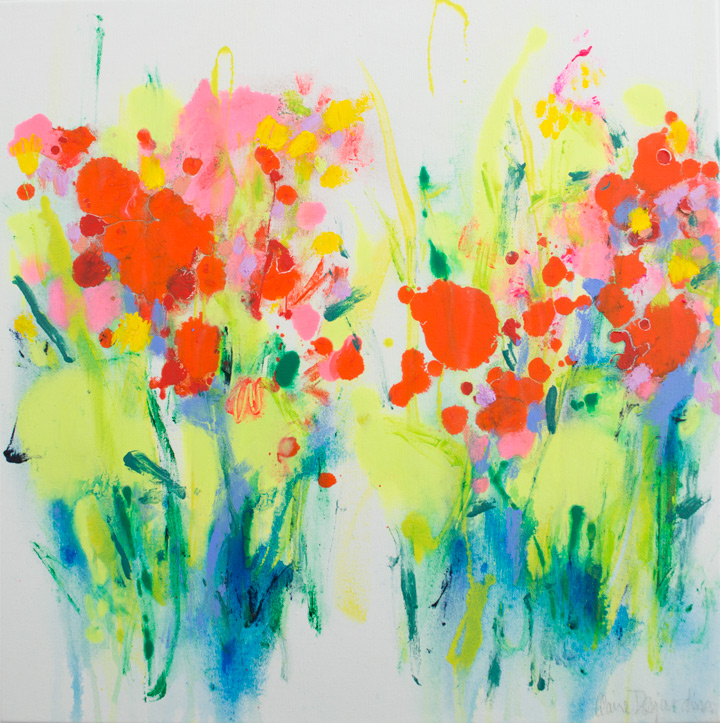
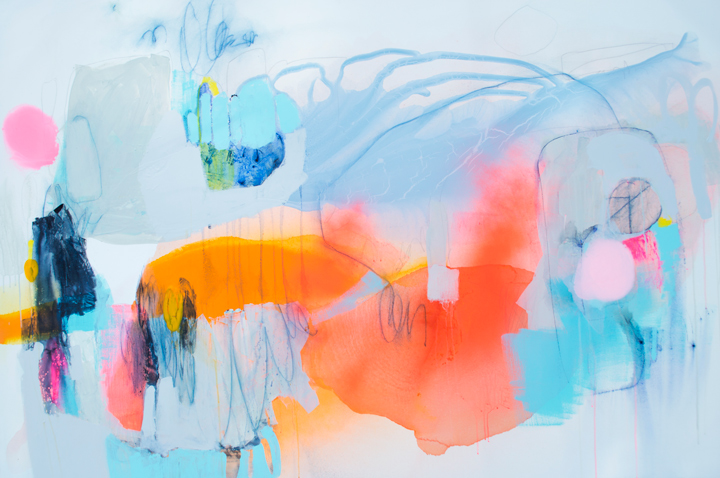
Debra’s work is made from porcelain clay. Porcelain is a very gracious medium but it is also equally demanding, which is why it is often given the analogy of “working with cream cheese.” Nonetheless, Debra prides herself from such difficulty, and furthermore, creates each one of her pieces from an original design. In fact, her vessels are still thrown on the initial wheel she purchased in 1974 at the age of 18. It was at such a young age that Debra began her journey of self-taught craftsmanship and throughout the years she has refined and mastered her trade. Debra Steidel’s work exhibits a uniquely unorthodox approach to porcelain, free from outside influence or conventional monotony. Debra Steidel lives, loves, and works in Wimberley, Texas, the heart of Hill Country located just southwest of Austin. She currently works out of her newly renovated studio.
The majority of Debra’s pieces contain interdependent vessels and lids. The lids are sculpted by hand, drawing inspiration from Debra’s love for nature, animals, and birds, but also containing more archaic influences from fossils, shells and bones. The surreal, symbiotic bond that forms between the vessels and lids creates a mesmerizing display. Yet, the true beauty of Debra’s pieces is rooted in the techniques of her creative process, more specifically, the crystalline glazing method of firing her vessels and the whimsical, handcrafted nature of her lids.
Debra’s whole process begins with a clump of slippery and soggy porcelain in her hands. Then, she starts forming it into a “vessel” on her potter’s wheel, a process also referred to as “throwing.” When the pot finally transforms into a leather hard state, a “foot” is trimmed on the bottom that refines the profile of the vessel. Once thoroughly dry, Debra places the vessels into a kiln oven to be heated to a low temperature creating a “bisque,” or model. The kiln hardens the pots just enough to handle the subsequent glazing process.
It is in the final glazing method of Debra Steidel’s work where the ultimate transcendence occurs. She chooses from a variety of distinct glazes to capture the precise sensation she chooses for each specific work. For example, she uses a metallic glaze to closely imitate the appearance of bronze, seemingly changing the composition of the material itself. More notably, the “Crystalline” glaze has one of the most astonishing effects ever achieved with porcelain.
The name “Crystalline” is derived from the actual crystal formation that occurs on the surface of the pieces during the kiln firing stage. This particular glazing process requires a complex combination of techniques including adding specific ingredients to the glaze formula, firing at extreme temperatures within the kiln, and orchestrating a series of specific temperature holds and slow cooling methods. In perfecting these techniques, Debra creates stunning patterns that make each piece uniquely different from the next. The perplexity of the “Crystalline” process can only be compared to the eccentricity of frost growing on a windowpane, a phenomenon that encapsulates the one-of-a-kind allure that all of Debra Steidel’s art pieces exude. It can be a very challenging process but when everything falls into place, the elegance of the piece never fails to amaze.
Artist Name
“The perplexity of the “Crystalline” process can only be compared to the eccentricity of frost growing on a windowpane, a phenomenon that encapsulates the one-of-a-kind allure that all of Debra Steidel’s art pieces exude. It can be a very challenging process but when everything falls into place, the elegance of the piece never fails to amaze.”